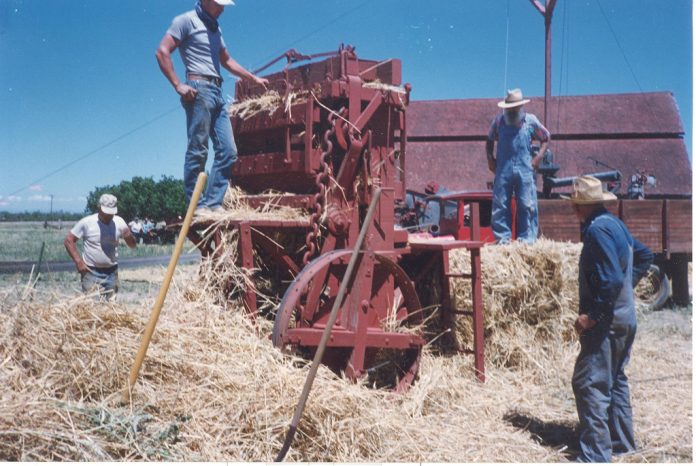
Good news! Finding the right square baler just got easier, according to Hesston by Massey Ferguson.
A blurb under the “New Products” column in a recent Farm and Dairy caught my eye, in which was described the new “standardized classification system for small and large square balers.”
Hesston
Hesston Manufacturing Company was started in 1947 in Hesston, Kansas, by Lyle Yost, to build a new auger grain unloader for combines.
In those days most combines had high-up grain bins that unloaded by gravity, slowing down the harvest.
Yost and a blacksmith friend developed an unloading auger and made five of them.
Yost’s cousin, Earl Burner, went out to sell them, got rid of all five in about three hours and could have sold more.
During the next harvest, others saw the speed and ease with which Yost’s augers unloaded grain bins, orders poured in from around the country and Hesston Manufacturing was born.
The firm soon branched out and began building self-propelled windrowers and the StakHand hay harvester.
The StakHand was an interesting closed-trailer like machine that picked up loose hay from the windrow, compressed it into a round topped stack that measured 8 feet wide, 14 feet long, and 10 feet high. Special StakMovers or StakFeeders were available to later handle the stacks.
In the early 1970s, Yost employed more than 2,500 workers and business was good, but the severe agricultural downturn in 1976 brought heavy losses.
Fiat bought controlling interest in the Hesston firm in 1977 and acquired the rest ten years later. Fiat eventually became part of ACGO and that’s where Hesston is today.
ACGO and Hesston’s “standardized classification system” uses load sensors to measure the force against the hay by the baling plunger measured in kNs or kilonewtons (each kilonewton equals 224.8 pounds of force) and the number of kNs is displayed on a monitor in the tractor cab for the operator’s information.
The classifications range from Class 1 (15 to 44 kNs which results in a 14’’ by 18” bale weighing from 50 to 85 pounds) that is said to be “ideal for equine operations, all the way up to Class 8 for “biomass operations,” a 3-foot by 4-foot bale weighing 1,400 to 2,000 pounds, and produced by 750+ kNs at the plunger.
Hay history
Until the early 19th century, most hay was put up loose but increased demand from city dwelling horse owners and livery stables, with limited storage space, sparked the need for compressing the forage.
Then, too, cotton was much easier to handle, store and transport when compressed into bales.
The earliest patent I can find for a “hay press,” or baler was issued in 1828 to M.B. Bliss of Pittston, Maine.
Others followed throughout the rest of the 19th century, with P.K. Dederick, of Albany, N.Y., being given credit for developing in 1872 the continuous hay press, a concept which is still used today. Prior to this, hay presses made only one bale at a time.
George Ertel, in Quincy, Illinois, also made many contributions to the manufacturing of balers.
Price press
During the 1860s, Jacob Price of Petaluma, California, began building an upright, single bale at a time press that used a horse-powered mechanism to force the follower upward, compressing the hay, cotton or other material to be baled in a sturdy wooden box at the top of the machine.
In Price’s 1863 patent, he described the operation of his press, which I’ll paraphrase: The follower is lowered, the lid or top door is opened, as is the side door above the platform.
The press box is then filled up to the level of the side door which is then closed and fastened.
The press box is entirely filled and the top is closed and secured.
The large wheel is then turned by an animal pulling a rope wound around its periphery, which is grooved for the purpose.
The wheel turns a grooved head, around which is wrapped a chain, at each end of its axle.
As the chains are wound on the heads, they draw down the toggle levers and force up the follower, which compresses the substance within the press box.
When compressed, the bale is bound in the usual manner, the side door is opened and the bale is forced out of the press box.
The bales made by the Jacob Price press, better known as the Petaluma Press, were about four feet long and maybe 18 by 18 inches square and weighed around 250 pounds. One source claims the bales were tied with five wires or bands, but I’ve never been unable to verify that.
Progress
Baler technology progressed to portable versions on wheels and from wooden to steel construction. Rotary horse-powered balers were popular during the later 1800s and many were equipped with pulleys so they could be driven by steam traction engines and later gas tractors.
In the early 1930s, George Innes, of Davenport, Iowa, put together pickup balers using tying mechanisms from grain binders and sold one to Ed Nolt, a custom operator from New Holland, Pennsylvania, who needed something to bale straw behind his combine.
Well, the thing didn’t work, but Nolt tinkered and modified the Innes machine until he had a pickup baler that worked well.
As many of you know, Nolt’s baler (some of you may recall the big, heavy New Holland 76 balers) was the beginning of the famous New Holland line of farm equipment that is still going strong as part of a huge global conglomerate called CNH Industrial.
So the history of hay baling is long and varied, and I’d be willing to bet that not P.K. Dederick, George Ertel, Jacob Price nor Ed Nolt ever once gave a thought as to how many kilonewtons of force it takes to make a bale.